In the fast-paced world of manufacturing and packaging, ensuring product safety and quality is critical. Metal detection plays a vital role in maintaining the integrity of packaged goods, especially foil-packaged goods. This article explores the benefits and uses of metal detectors in aluminum packaging, shedding light on this critical aspect of the packaging industry.
Aluminum foil packaging offers many benefits, including excellent barrier properties, extended shelf life and resistance to moisture, gas and light. These benefits make it a popular choice for everything from food and beverages to pharmaceuticals and electronics. However, the presence of metallic contaminants may affect the quality and safety of packaged goods.
This is where metal detection technology comes into play. Metal detectors are electronic devices specifically designed to identify the presence of metal objects within packaged products, such as aluminum foil packages. These devices utilize advanced sensing technology to accurately detect and locate even small metal particles. They can effectively identify a variety of metal contaminants, including ferrous metals, non-ferrous metals and stainless steel.
The main purpose of aluminum packaging metal detection is to ensure that the packaged products do not contain any metallic foreign matter. This is critical to preventing metal contaminants from causing potential harm to consumers. For example, in the food industry, metal contamination can cause serious health risks if consumed unknowingly. By incorporating metal detectors into the packaging process, manufacturers can significantly reduce the likelihood of such incidents occurring.
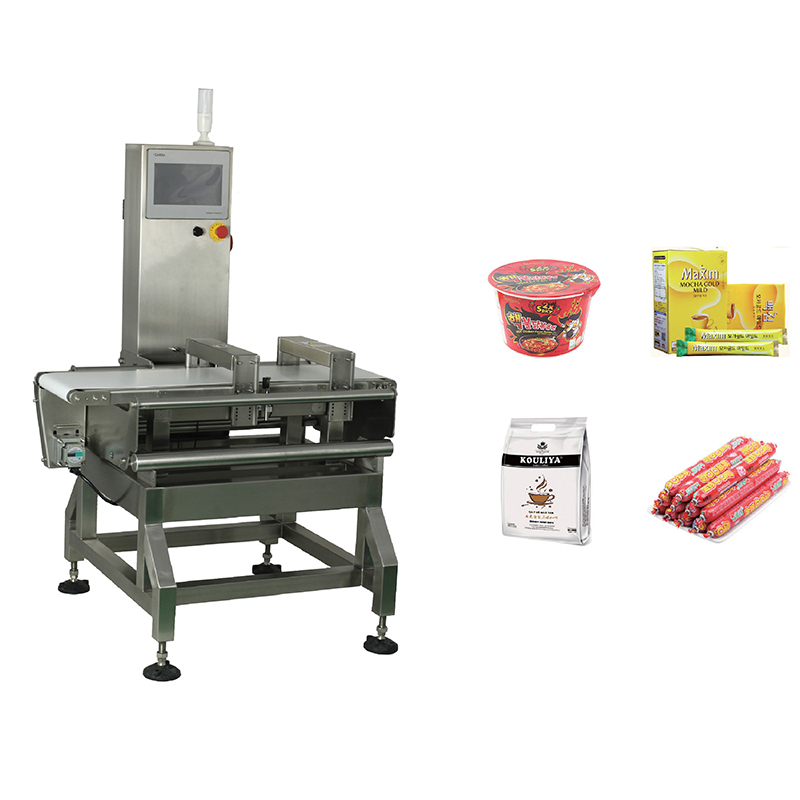
Metal detection is particularly important in industries where high standards of product quality and safety are crucial. Industries such as pharmaceuticals and electronics rely heavily on aluminum foil packaging to protect their products from external factors. Detection and elimination of any metallic impurities during the packaging process is critical to maintaining the quality and performance required for these sensitive commodities.
One of the main advantages of aluminum packaging metal detection is the ability to operate at high production speeds without compromising accuracy. Modern metal detectors are equipped with advanced algorithms and state-of-the-art sensors to quickly detect metal contaminants as products pass through conveyor belts. This ensures that the packaging process remains efficient and does not create any bottlenecks in the production line.
Additionally, metal detection technology often features user-friendly interfaces and intuitive controls that allow operators to easily set up and monitor detection parameters. These devices can be seamlessly integrated into existing production lines and run smoothly without major modifications.
Additionally, metal detection not only protects the end consumer but also protects the manufacturer’s brand reputation. A single incident of metal contamination due to inadequate testing measures can have serious consequences, including product recalls, litigation and loss of consumer trust. By implementing a robust metal detection system, manufacturers can demonstrate their commitment to quality assurance and product safety, thereby strengthening their brand image.
To sum up, metal detection plays a vital role in ensuring the safety and quality of aluminum foil packaging products. By effectively identifying and eliminating metal contaminants, these devices help prevent hazards, maintain product integrity, and safeguard consumer health. Metal detectors have become an indispensable tool in the packaging industry due to their high-speed operation, user-friendly interface and brand protection advantages. Manufacturers across industries must prioritize integrating reliable metal detection systems to meet regulatory requirements and ensure customer satisfaction.
Post time: Oct-24-2023